AgLogic™
- Improve asset utilization by electronically assigning work orders to application equipment.
- Make better scheduling decisions by seeing the entire equipment fleet on a single map.
- Use advanced reporting to analyze machine and operator performance.
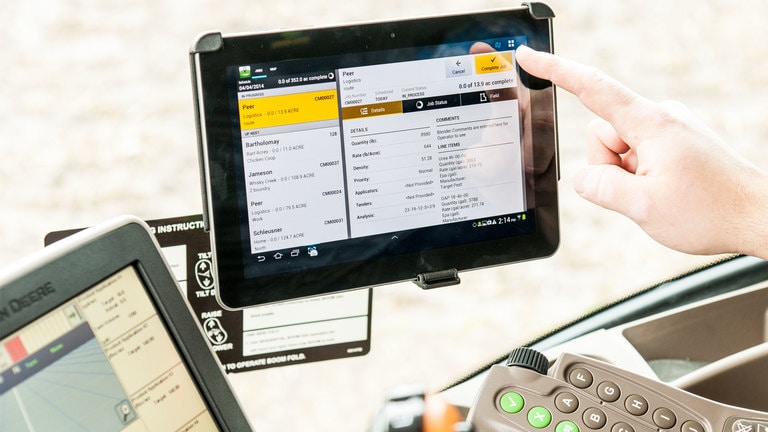
Features
Manage work orders to improve asset utilization


The schedule and dispatch feature enables the scheduling and re-prioritization of work orders to an applicator and its supporting tenders:
- Provides visibility of all work orders simultaneously
- Shows all work orders georeferenced, using field boundary information
- Allows operator to assign work orders to equipment, including the application and tender
- Optimizes the routes for selected equipment
- Improves office efficiency by scheduling with a web-based system that automatically sends work order information to the operator in the field
- Schedule work orders based off product, customer, and location details
- Assign multiple applicators to the same work orders
- Utilize the advanced filter option to sort orders by client, farm, field, crop, product, dates, order numbers, priority, types, location, or rates
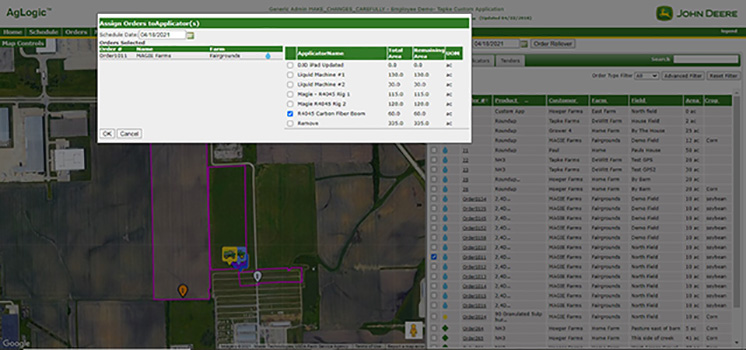
Improve risk management

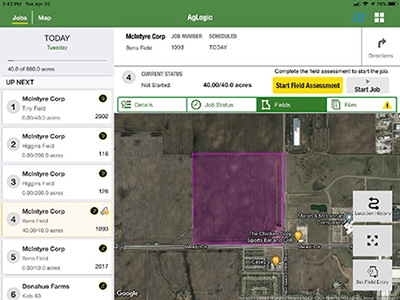
AgLogic™ system improves capabilities to manage risk, making sure the right resources get to the right place at the right time.
- AgLogic solution can easily sort out work orders based on product to be applied. The scheduler can quickly schedule the same product application to the same applicator, reducing the need to rinse out and risk of contamination.
- Schedulers and operators can easily view weather conditions such as air temp, wind direction, wind speed, and radar in motion to know if applicators will be affected and quickly adjust schedules.
- Weather conditions prepopulate at the start and finish of each work order.
- Driving directions — applicators and tender drivers can get driving directions to field entry points.
- Field view on tablet allows the operator to confirm the correct field is being worked.
- DriftWatch™ sensitive crop registry allows both the scheduler and operator to see where sensitive crop locations are in relation to scheduled work as well as contact info for the grower.
DriftWatch is a trademark of Purdue Research foundation.
Track equipment and associated activities
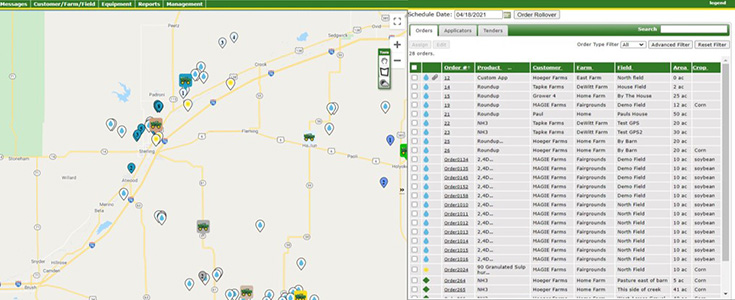
Use the AgLogic™ web application to view the current location of assets. The GPS position is updated one time per minute, providing the scheduler with valuable machine location and status.
- Provides a visual representation of the entire trade area and fleet, or the specific region associated with the user's secure login
- Helps make educated scheduling and routing decisions with a simple visual representation of operational activities to optimize allocation and the use of resources: equipment, people, and time
- Reduces the cost of applicator downtime by scheduling tenders based on their location in relation to the order, applicator, and/or blender locations
- Minimize tender refill time with geofences that alert the blend plant of incoming tenders
- Protects the Ag retailer’s business against disputes by confirming the location of completed work orders
- Completed work order tickets are customizable with more than 60 different conditions that managers may require applicators to document
Send work order information wirelessly
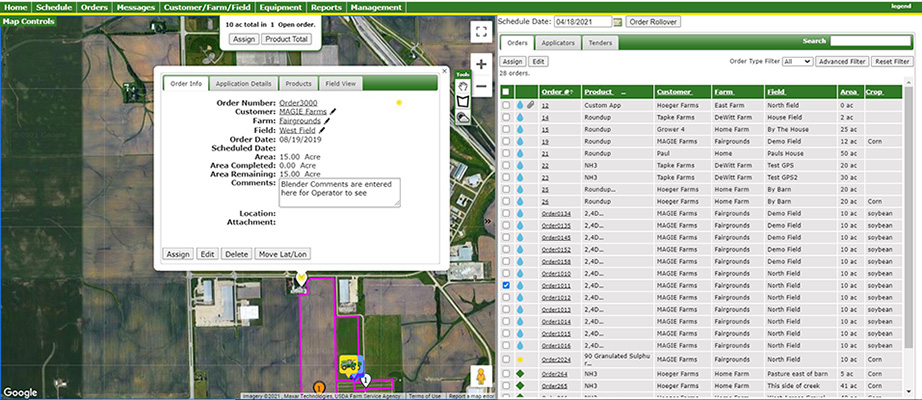
Automated data transfer functionality sends work order information from the AgLogic™ web application to the field and completed work order information from the field back to the web application:
- Allows user to react to schedule changes and immediately reroute assets by automatic communication to the field
- Reduces trips to the office and increases completed acres per day by receiving work instructions in the field electronically
- Increases the number of tendered applicators by enabling real-time schedule changes and enabling tenders to start their day in the field
- Improves cash flow by invoicing upon receipt of completed, adjusted work order information from the field
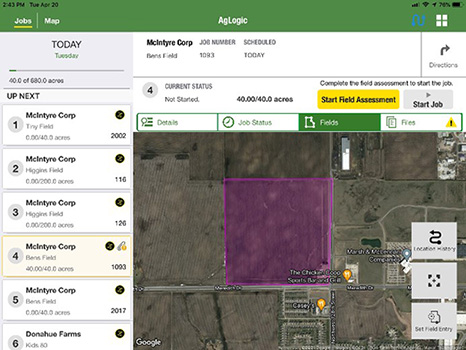
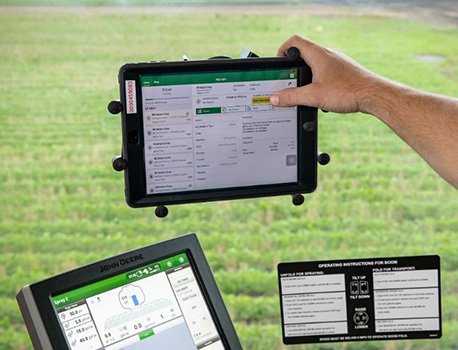
Transmit files electronically to the field
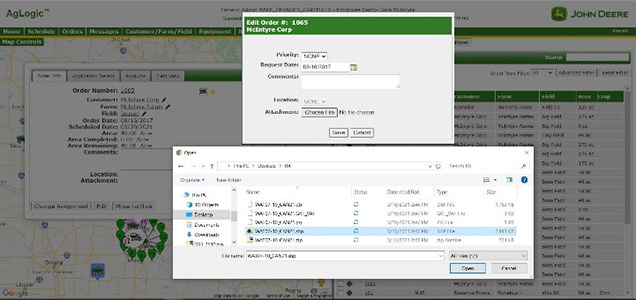
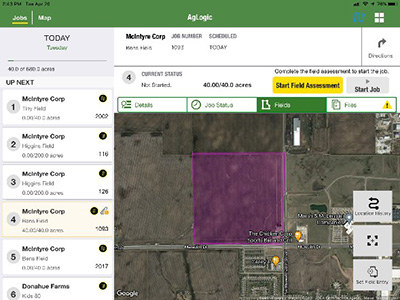
File transfer enables two-way file transfer between the office and the field. The AgLogic™ solution can wirelessly send a prescription file directly to the mobile device in the cab. When the file is received, the operator is prompted that a file is attached to the work order. The file can then be moved from the mobile device to any supported display via a USB stick or John Deere Mobile Data Transfer. If a work order is assigned to an applicator that is equipped with a Generation 4 display and JDLink, then the prescription file will automatically be sent from AgLogic to the display. Raven Slingshot® displays may also accept assigned work orders and prescriptions wirelessly from AgLogic. Prescriptions may also be sent directly from supported back-offices without being uploaded.
As-applied data can be attached to the work order in the applicator cab. The as-applied data is stored with the completed work order in the AgLogic system and can be migrated to other back-office software applications.
NOTE: File transfer is available with the AgLogic Advanced license only.
File transfer provides the following benefits:
- Reduces out-of-office time by wirelessly transferring files to the field
- Reduces downtime in the field by wirelessly receiving and sending files as needed
Slingshot is a trademark of Raven Industries, Inc
Get turn-by-turn directions to scheduled fields
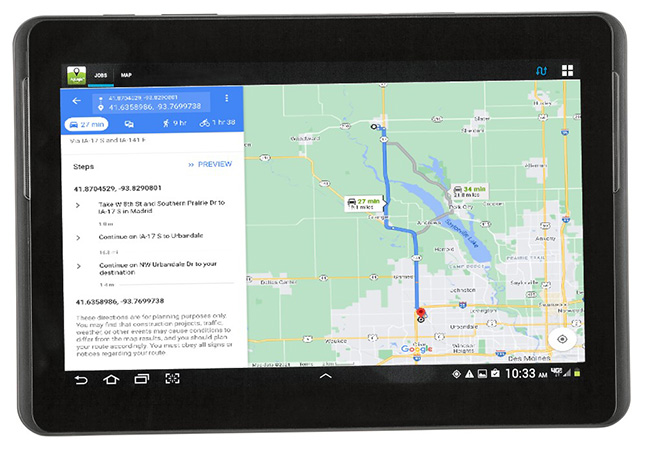

The AgLogic™ solution provides turn-by-turn directions to any field or facility associated with the work order. Schedulers and managers may also view and track operators from the website to verify current location and status.
Driving directions
- Saves time and eliminates paper waste at the plant by electronically guiding operators to fields
- Schedules may pin the entry point of each field for more accurate driving directions
- Eliminates time-robbing errors by providing turn-by-turn directions to operators in route to the field
- Increases tender productivity by providing turn-by-turn directions for tender drivers who are not familiar with field locations
- Allows new operators confidence and increased efficiency getting to the field
- Prevents unnecessary phone calls
- Helps to avoid costly misapplication
Analyze efficiency reports
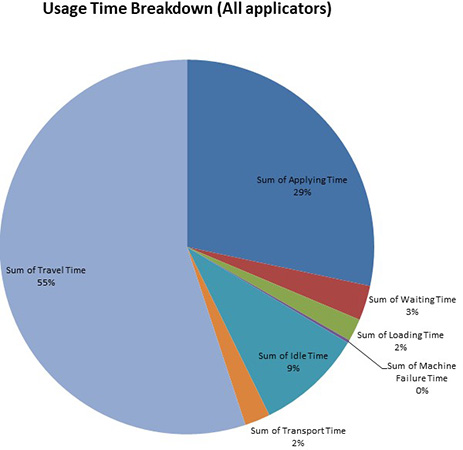

- Make informed management decisions with supporting data
- Analyze individual operator/machine productivity
- Identify which machines are most productive with acres/hour covered by machine or operator
- Reduce inefficiency when the producer can measure how much time is spent idling or waiting on tenders
- Identify efficiency gaps such as a need for more equipment or tenders
Specifications
The AgLogic™; available at all the following C & B Locations:
- Billings, MT
- Blackfoot, ID
- Jackson, MN
- Lake Park, IA
- Chamberlain, SD
- Edgerton, MN
- St. James, MN
- Luverne, MN
- Circle, MT
- Roscoe, SD
- Yankton, SD
- Freeman, SD
- Corsica, SD
- Miles City, MT
- Worthington, MN
- Culbertson, MT
- Rexburg, ID
- Gettysburg, SD
- Miller, SD
- Storm Lake, IA
- Wagner, SD
- Mitchell, SD
- Powell, WY
- Plentywood, MT
- Glasgow, MT
- Truman, MN
- Selby, SD
- Pipestone, MN
- Tracy, MN
- Glendive, MT
- Sheridan, WY
- Spencer, IA
- Slayton, MN
- Ida Grove, IA
- Sibley, IA
- Sioux Falls, SD (Ideal Yardware)
- Spirit Lake, IA
- Sioux Falls, SD (FSO Office)
- Idaho Falls, ID